Owijania - Wire wrap
Wire wrap to technika montażu podzespołów elektronicznych, która została wynaleziona do okablowania telefonicznych przełączników krzyżowych , a później została zaadaptowana do budowy obwodów elektronicznych . Elementy elektroniczne zamontowane na płycie izolacyjnej są połączone ze sobą odcinkami izolowanego przewodu biegnącego między ich zaciskami, przy czym połączenia wykonuje się poprzez owinięcie kilku zwojów nieizolowanych odcinków przewodu wokół przewodu komponentowego lub kołka w gnieździe.
Druty mogą być owijane ręcznie lub maszynowo, a następnie mogą być ręcznie modyfikowane. Był popularny w produkcji na dużą skalę w latach 60. i wczesnych 70. i nadal jest używany do produkcji krótkich serii i prototypów . Metoda eliminuje projektowanie i wytwarzanie płytki drukowanej . Owijanie drutem jest nietypowe wśród innych technologii prototypowania, ponieważ pozwala na produkcję złożonych zespołów za pomocą zautomatyzowanych urządzeń, a następnie łatwą naprawę lub modyfikację ręczną.
Konstrukcja owijki drutowej może wytwarzać zespoły, które są bardziej niezawodne niż obwody drukowane: połączenia są mniej podatne na uszkodzenia z powodu wibracji lub fizycznych naprężeń na płycie bazowej, a brak lutu wyklucza błędy lutowania, takie jak korozja, spoiny na zimno i połączenia suche. Same połączenia są sztywniejsze i mają niższą rezystancję elektryczną ze względu na spawanie drutu na zimno do słupka zaciskowego w rogach.
Do montażu prototypów wysokiej częstotliwości i niewielkich serii produkcyjnych, w tym gigahercowych obwodów mikrofalowych i superkomputerów, wykorzystano owijkę drucianą . Wyjątkowość wśród zautomatyzowanych technik prototypowania polega na tym, że długość przewodów może być dokładnie kontrolowana, a skręcone pary lub magnetycznie ekranowane skręcone czworokąty mogą być trasowane razem.
Konstrukcja owijana drutem stała się popularna w produkcji płytek drukowanych około 1960 roku, a obecnie jej użycie gwałtownie spadło. Technologia montażu powierzchniowego sprawiła, że technika ta jest znacznie mniej użyteczna niż w poprzednich dekadach. Lutowane mniej łączeniowe i zmniejszając koszt profesjonalnie wykonane zostały prawie wyeliminowane PCB tej technologii.
Przegląd
Prawidłowo wykonane połączenie owijane dla drutu 30 lub 28 AWG to siedem zwojów (mniej dla większego drutu) gołego drutu z pół do półtora zwoju izolowanego drutu na dole w celu odciążenia. Kwadratowy słupek pokryty twardym złotem tworzy zatem 28 zbędnych styków. Posrebrzana powłoka drutu zgrzewa się na zimno do złota. Jeśli wystąpi korozja, pojawia się na zewnątrz drutu, a nie na styku gazoszczelnym, gdzie tlen nie może przeniknąć, tworząc tlenki. Prawidłowo zaprojektowane narzędzie do owijania drutu przykłada do dwudziestu ton siły na cal kwadratowy na każde złącze.
Części elektroniczne czasami podłącza się do gniazd . Gniazda są mocowane za pomocą cyjanoakrylanu (lub kleju silikonowego ) do cienkich płytek z żywicy epoksydowej wzmocnionej włóknem szklanym ( włóknem szklanym ).
Gniazda mają kwadratowe słupki. Typowe słupki mają kwadrat 0,025 cala (0,64 mm), wysokość 1 cala (25,4 mm) i są rozmieszczone w odstępach 0,1 cala (2,54 mm). Słupki premium są wykonane z twardo ciągnionego stopu miedzi berylowej pokrytej złotem o grubości 0,000025 cala (630 nm), aby zapobiec korozji. Mniej kosztowne posty są z brązu z blaszanym poszyciem.
30 gauge (~ 0.0509mm 2 ) srebro -plated miękkiej miedzi przewód jest izolowany z fluoropochodnej węglowodoru , które nie wydzielają niebezpieczne gazy, przy ogrzewaniu. Najpopularniejszą izolacją jest „ Kynar ”.
Drut Kynar 30 AWG jest cięty na standardowe odcinki, a następnie z każdego końca usuwany jest jeden cal izolacji.
„Narzędzie do owijania drutu” ma dwa otwory. Przewód i 1 / 4 w (6,4 mm) izolowanego drutu są umieszczone w otworze w pobliżu krawędzi narzędzia. Otwór w środku narzędzia jest umieszczony nad słupkiem.
Narzędzie szybko się skręca. W rezultacie 1,5 do 2 zwojów izolowanego drutu jest owijanych wokół słupka, a powyżej 7 do 9 zwojów gołego drutu jest owijanych wokół słupka. W słupku jest miejsce na trzy takie połączenia, choć zwykle wystarczy jedno lub dwa. Umożliwia to ręczne owijanie drutów podczas napraw.
Półtora obrotu izolowanego drutu zapobiega zmęczeniu drutu w miejscu styku ze słupkiem.
Powyżej zwoju izolowanego drutu drut nieosłonięty owija się wokół słupka. Narożniki słupka wgryzają się pod naciskiem ton na cal kwadratowy. Wypycha to wszystkie gazy z obszaru między srebrną płytką drutu a złotymi lub cynowymi rogami słupka. Co więcej, przy 28 takich połączeniach (siedem zwojów na czworokątnym słupku) istnieje bardzo niezawodne połączenie między drutem a słupkiem. Ponadto narożniki słupków są dość „ostre”: mają dość mały promień krzywizny.
Istnieją trzy sposoby układania przewodów na płytce.
W profesjonalnie zbudowanych tablicach wire-wrap długie druty są umieszczane jako pierwsze, aby krótsze druty mechanicznie zabezpieczały długie druty. Ponadto, aby zespół był łatwiejszy do naprawy, druty są nakładane warstwami. Końce każdego drutu są zawsze na tej samej wysokości na słupku, więc co najwyżej trzy druty muszą zostać wymienione w celu wymiany drutu. Ponadto, aby warstwy były lepiej widoczne, wykonano je z różnymi kolorami izolacji. W zespołach owijanych drutem o parametrach kosmicznych lub zdatnych do lotu, przewody są zapakowane w pudełko i mogą być odpowiednio pokryte woskiem w celu zmniejszenia wibracji. Epoksyd nigdy nie jest używany do powlekania, ponieważ sprawia, że montaż nie nadaje się do naprawy.
Uwagi dotyczące aplikacji
Wire-wrap działa dobrze z układami cyfrowymi z niewielką liczbą elementów dyskretnych, ale jest mniej wygodny w przypadku systemów analogowych z wieloma opornikami dyskretnymi, kondensatorami lub innymi komponentami (takie elementy można przylutować do nagłówka i podłączyć do gniazda wire wrap). Gniazda stanowią dodatkowy koszt w porównaniu do bezpośredniego wstawiania układów scalonych do płytki drukowanej i zwiększają rozmiar i masę systemu. Wiele pasm drutu może wprowadzać przesłuchy między obwodami, co ma niewielkie znaczenie dla obwodów cyfrowych, ale stanowi ograniczenie dla systemów analogowych. Połączone przewody mogą emitować zakłócenia elektromagnetyczne i mają mniej przewidywalną impedancję niż płytka drukowana. Konstrukcja wire-wrap nie może zapewnić płaszczyzn uziemienia i płaszczyzn dystrybucji mocy z wielowarstwowymi płytkami drukowanymi, zwiększając prawdopodobieństwo wystąpienia szumów.
Historia

Owijanie drutem wywodzi się z tradycji zaplatania lin . Wczesne owijanie drutu odbywało się ręcznie; powolny i ostrożny proces. Owijanie drutu było używane do połączeń i do wykańczania końców kabli w drutach mostów wiszących i innych olinowaniu linowym, zwykle z drutem o mniejszej średnicy owiniętym wokół większego drutu lub wiązki drutów. Takie techniki były czysto mechaniczne, aby dodać siły lub zapobiec strzępieniu się.
Pod koniec XIX wieku dyżurni telegraficzni opracowali metody wykonywania spawów, które byłyby wytrzymałe mechanicznie, a także przewodziły elektryczność. Splice Western Union był najsilniejszym z tych spawów drutu owinięty. Opaski można pokryć lutem, aby uzyskać jeszcze większą wytrzymałość i zapobiec utlenianiu między drutami.
Ręcznie owijane przewody były powszechne na początku XX wieku w metodach budowy elektroniki punkt-punkt , w których potrzebne było silne połączenie, aby utrzymać komponenty na miejscu. Druty były ręcznie owijane wokół słupków zaciskowych lub łopatek, a następnie lutowane.
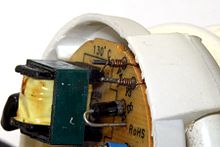
Nowoczesna technologia wire wrapping została opracowana po II wojnie światowej w Bell Laboratories jako sposób wykonywania połączeń elektrycznych w nowym przekaźniku projektowanym do zastosowania w systemie Bell Telephone. Zespół projektowy kierowany przez Arthura C. Kellera opracował „Keller Wrap Gun”, a cały system owijania został przekazany firmie Western Electric do zastosowań przemysłowych. Po tym, jak komisja „wyprodukuj lub kup” w Western Electric zdecydowała, że narzędzie ręczne zostanie wyprodukowane przez zewnętrznego dostawcę, Western Electric wysłała kontrakt na narzędzia do przetargów. Keller Tool z Grand Haven w stanie Michigan, dostawca obrotowych narzędzi ręcznych dla Western Electric, wygrał kontrakt i wprowadził kilka zmian konstrukcyjnych, aby narzędzie było łatwiejsze w produkcji i obsłudze. Keller rozpoczął produkcję narzędzi w 1953 roku, a następnie uzyskał licencję Western Electric pozwalającą na sprzedaż technologii na wolnym rynku. Narzędzie sprzedawano pod oryginalną nazwą – ponieważ nazwa producenta przypadkiem pokrywała się z nazwiskiem wynalazcy.
Pierwsze komputery tranzystorowe IBM , wprowadzone w późnych latach pięćdziesiątych, zostały zbudowane przy użyciu standardowego systemu modułowego IBM, który wykorzystywał płyty montażowe owinięte drutem.
Ręczne owijanie drutu

Ręczne narzędzie do owijania drutu przypomina mały długopis. Jest wygodny przy drobnych naprawach. Drut wrap to jeden z najłatwiejszych do naprawy systemów do montażu elektroniki. Słupki można owijać do dziesięciu razy bez znacznego zużycia, pod warunkiem, że za każdym razem używany jest nowy drut. Nieco większe prace wykonuje się za pomocą ręcznego „pistoletu do owijania drutu” z przekładniowym i sprężynowym uchwytem ściskającym, aby szybko obracać bitem.
Takie narzędzia były używane masowo w amerykańskich centralach telefonicznych w ostatniej trzeciej połowie XX wieku, zwykle z większym bitem do obsługi przewodu 22 lub 24 AWG, a nie mniejszym 28 lub 30 AWG stosowanym w płytkach drukowanych i płytach montażowych. Większe posty można przepakowywać setki razy. Przetrwały do XXI wieku w rozdzielnicach, w których łączniki izolacyjno-przesuwne nie przejęły w całości. Większe, ręczne, szybkie elektryczne pistolety do owijania zastąpiły lutowanie pod koniec lat 60. w przypadku stałego okablowania podczas instalowania sprzętu do wymiany. W połowie lat 80. były stopniowo zastępowane przez kable konektorowe.
Apollo Guidance Computer , z jego krótką metę produkcji oraz rygorystyczne wymagania niezawodności, był jednym z pierwszych zastosowań owinąć przewód do montażu komputera.
Półautomatyczna owijka druciana

Półautomatyczne, zasilane systemy wire-wrap umieszczają „pistolety wire-wrap” na ramionach poruszanych w dwóch wymiarach za pomocą sterowanych komputerowo silników. Pistolety są ręcznie ściągane, a spust wciskany w celu zawijania. Przewody są wprowadzane do pistoletu ręcznie. System ten pozwala operatorowi na umieszczenie przewodów bez obaw o to, czy znajdują się na właściwym sworzniu, ponieważ komputer prawidłowo umieszcza pistolet.
Półautomatyczne owijanie przewodów jest wyjątkowe wśród systemów prototypowania, ponieważ może umieszczać skręcone pary i skręcone magnetycznie ekranowane quady, co pozwala na montaż złożonych obwodów radarowych i cyfrowych o dużej prędkości.
Automatyczne owijanie drutu
Zautomatyzowane owijarki do drutu, produkowane przez firmę Gardner Denver w latach 60. i 70. XX wieku, były zdolne do automatycznego trasowania, cięcia, zdejmowania izolacji i owijania przewodów na elektroniczną „płytę montażową” lub „płytkę drukowaną”. Maszyny były napędzane przez okablowanie instrukcje kodowane na kartach perforowanych , Mylar perforowane taśmy dziury i wczesne mikro komputerów.
Najwcześniejsze maszyny (na przykład modele 14FB i 14FG) były początkowo skonfigurowane jako „poziome”, co oznaczało, że płyta do owijania drutu była umieszczana do góry nogami na poziomej płycie narzędziowej, którą następnie zwijano do maszyny i blokowano na obrotowy (pozycja obrotowa stołu TRP w czterech pozycjach) i przesuwny (PLP = pozycja wzdłużna palety w 11 pozycjach) zespołu palet. Maszyny te zawierały bardzo duże jednostki hydrauliczne do zasilania serw, które napędzały wózki napędowe „A” i „B” montowane na śrubie kulowej, szafę z elektroniką o wysokości 6 stóp (1,8 m) załadowaną setkami przekaźników sterujących IBM, wieloma dziesiątkami elektrozaworów dla sterowanie różnymi pneumatycznymi podsystemami mechanicznymi oraz czytnik kart IBM 029 do pozycjonowania instrukcji. Same automatyczne owijarki do drutu były dość duże, 6 stóp (1,8 m) wysokości i 8 stóp (2,4 m) kwadratu. Obsługa maszyn była niezwykle skomplikowana i często oznaczała wchodzenie do nich tylko po to, by nad nimi pracować. Mogłoby to być dość niebezpieczne, gdyby blokady bezpieczeństwa nie były odpowiednio konserwowane.
Później nieco mniejsze maszyny były „pionowe” (14FV), co oznaczało, że płyty były umieszczane na płycie narzędziowej z kołkami skierowanymi do operatora maszyny. Zniknęły jednostki hydrauliczne, na rzecz silników z napędem bezpośrednim do obracania śrub kulowych , z enkoderami obrotowymi zapewniającymi sprzężenie zwrotne pozycjonowania. Generalnie zapewniało to lepszą widoczność produktu dla operatora, chociaż maksymalna powierzchnia owijania była znacznie mniejsza niż w przypadku maszyn poziomych. Najwyższe prędkości na maszynach poziomych wynosiły na ogół około 500-600 drutów na godzinę, podczas gdy maszyny pionowe mogły osiągać szybkość nawet 1200 na godzinę, w zależności od jakości płytki i konfiguracji okablowania.
Automatyzacja projektowania
W wire-wrapping automatyzacja projektowania elektronicznego może zaprojektować płytkę i zoptymalizować kolejność umieszczania przewodów.
Niektóre systemy były w stanie zaakceptować projekty logiki wysokiego poziomu napisane w języku projektowania podobnym do VHDL lub Verilog i kompilować projekty, aby automatycznie wygenerować schemat i zestawienie materiałów. Zwykle umożliwiają one symulację i debugowanie projektów logicznych przed faktycznym zbudowaniem obwodów logicznych.
CAD dla wire-wrap wymaga, aby schemat był zakodowany w netlistę. Lista sieci jest koncepcyjnie listą pinów, które powinny być połączone, z powiązaną nazwą sygnału dla wszystkich pinów, które dotykają sygnału. Ten krok, często wykonywany ręcznie w starszych systemach, jest teraz wykonywany automatycznie przez programy EDA, które wykonują „przechwytywanie schematów”. Ręczne adnotacje są zwykle nadal wymagane w przypadku sygnałów specjalnych, takich jak szybkie, wysokoprądowe lub czułe na szum obwody, lub specjalnych technik konstrukcyjnych, takich jak skrętki lub specjalne trasowanie. Adnotacje są zakodowane w polu każdego rekordu listy sieci.
Następnym krokiem było zakodowanie pozycji pinów każdego urządzenia. Jeden łatwy sposób zakodował pozycję wierszy z literami i ponumerowanych kolumn. Urządzenia i piny zostały następnie przemianowane z nazw typu U36-2, tj. pin 2 układu scalonego numer 36, na nazwy typu A01-2, dla pinu 2 układu scalonego w rzędzie A, kolumna 01. Technik za pomocą precyzyjnej linijki mierzy odległości rzędów i kolumn od wywierconego otworu w tablicy i wprowadza pomiar do pliku.
Typ każdego urządzenia jest również wprowadzany w innym pliku, powiązanym z nazwą urządzenia. Np. A01 jest identyfikowany jako 74C00.
Następnie program komputerowy „rozbija” listę urządzeń, współrzędne i opisy urządzeń w kompletną listę pinów dla płytki przy użyciu szablonów dla każdego typu urządzenia. Szablon to mapa pinów urządzenia. Można go zakodować raz, a następnie udostępnić wszystkim urządzeniom tego typu.
Niektóre systemy mogą następnie zoptymalizować projekt, eksperymentalnie zamieniając pozycje równoważnych części i bramek logicznych w celu zmniejszenia długości przewodu. Po każdym ruchu należy zmienić nazwę powiązanych pinów na liście sieci.
Niektóre systemy automatycznie wykrywają również piny zasilania w układach scalonych i generują netlisty łączące je z najbliższymi pinami zasilania na płycie. Jeśli tak się stanie, można przypisać dowolne specjalne adnotacje lub kolory (np. biały dla sygnałów zegara lub czerwony dla zasilania), ponieważ programy te mają dogłębną wiedzę na temat pinów układu scalonego.
Następnie program komputerowy sortuje zarówno listę sieci, jak i listę pinów w kolejności alfabetycznej według nazwy pinów. Następnie odczytuje obie listy. Gdy nazwa pinu na liście sieci pasuje do nazwy pinu na liście pinów, kopiuje fizyczne współrzędne z listy pinów do listy sieci.
Lista sieci jest następnie porządkowana według nazwy sieci, tak aby wszystkie piny każdej sieci były razem. Następny program zmienia kolejność kołków w każdej sieci, aby skrócić przewody. Zmniejsza to koszt płyty poprzez skrócenie długości przewodów. Pozwala również na szybsze sygnały poprzez zmniejszenie pojemności sieci i zużywa mniej energii poprzez zmniejszenie rezystancji każdego przewodu. Gdy potrzebne są wysokie prądy, rozmiary przewodów można zmniejszyć o połowę (lub można zastosować standardowe rozmiary przewodów cyfrowych dla wyższych prądów), prowadząc sieci jako koła, a nie sekwencje. Niektóre szybkie sygnały wymagają sterownika na jednym końcu i rezystora na drugim, aby pochłaniały odbicia.
Ten problem marszruty jest równoważny problemowi komiwojażera , który jest NP kompletny i dlatego nie można go rozwiązać w rozsądnym czasie. Jednym z praktycznych algorytmów routingu jest wybranie pinu znajdującego się najdalej od środka płytki, a następnie użycie algorytmu zachłannego do wybrania najbliższego nieroutowanego pinu o tej samej nazwie sygnału.
Po trasowaniu każda para węzłów w sieci zostaje przepisana, aby stać się przewodem, na „liście przewodów”. Ponieważ lista styków sygnałowych jest przepisana jako lista przewodów, program może przypisać atrybuty w rekordach, aby wskazać, czy przewód jest górny czy dolny. To proste: zacznij od dołu. Następny drut jest na górze. Następny przewód to dolny itd. Ponieważ przyporządkowane są przewody dolne i górne, można im również przypisać wybrane kolory przewodów dolnych i górnych. Zazwyczaj niebieski jest używany do dolnych przewodów, a żółty do górnych przewodów. Taki układ umożliwia ręczną naprawę lub modyfikację z usunięciem co najwyżej trzech przewodów.
Po tym, tablica o losowym routingu może mieć rozmiary przewodów obliczone jako odległość między pinami, plus odległości na każdym końcu, plus procent (zwykle 5%) dla luzu.
Jeśli przewody muszą być poprowadzone liniami (wymagane w przypadku niektórych sygnałów o wysokiej częstotliwości lub niskim poziomie szumów), osobny program do trasowania odczytuje plik „pasów”, aby znaleźć miejsce, w którym przewody poprowadzone torami mogą być umieszczone na płycie. Następnie wstawia „polecenia palcami” do każdego rekordu drutu, dzięki czemu zautomatyzowane owijarki lub technicy montażowi mogą umieścić korpus drutu na linii trasowania. Jednocześnie przelicza długość przewodu, aby można go było prawidłowo poprowadzić.
Jeśli płytka ma być poprowadzona ręcznie, co jest potrzebne w przypadku nietypowych instrukcji trasowania, skrętek i czterożyłowych oplotów magnetycznych, rozmiary przewodów są przerabiane na standardowe rozmiary. Pozwala to technikowi montażowemu na pobieranie przewodów z pojemników z wstępnie oczyszczonym drutem o standardowej długości.
Lista przewodów jest następnie sortowana alfabetycznie według optymalnej kolejności montażu. Przewody dolne są umieszczone przed przewodami górnymi. Długie przewody są zwykle umieszczane jako pierwsze na poziomie, aby krótsze przewody przytrzymywały dłuższe przewody. Zmniejsza to wibracje dłuższych przewodów, dzięki czemu płyta jest bardziej wytrzymała w wibrującym środowisku, takim jak pojazd. Jednoczesne umieszczenie wszystkich drutów o określonym rozmiarze i poziomie ułatwia montażyście korzystanie z wstępnie przyciętych, wstępnie odizolowanych drutów podczas korzystania z półautomatycznej owijarki drutowej. Druty o różnych kolorach, ale o tym samym rozmiarze są również sortowane, aby można je było połączyć. Sporządzony jest wykaz przewodów i innych elementów potrzebnych do montażu, który jest sortowany i drukowany do użytku przez operatorów maszyn, a następnie przekształcany w taśmę lub talię kart dla maszyny. Ta aukcja pozwala również na montaż materiałów przed uruchomieniem produkcyjnym.
W przypadku ręcznego i półautomatycznego owijania drutu kierunek umieszczania drutu można zoptymalizować pod kątem operatorów praworęcznych , tak aby druty były umieszczane od prawej do lewej. W pełni zautomatyzowane owijarki drutowe nie dbają o to. Ale w półautomatycznym systemie owijania drutu, powoduje to odsunięcie głowicy owijarki od dłoni użytkownika podczas umieszczania drutu. Zwiększa to bezpieczeństwo. Pomaga również użytkownikowi użyć silnej ręki i oka do poprowadzenia przewodu. Inna optymalizacja polega na tym, że w obrębie każdej długości i koloru drutu komputer wybiera następny drut, tak aby głowica owijająca przesunęła się do najbliższego kołka, który znajduje się na prawo od poprzedniego kołka. Pozwala to zaoszczędzić do 40% czasu montażu, prawie uzyskując dwie maszyny do owijania drutu w cenie jednej. Zmniejsza również zużycie owijarek do drutu i pozwala technikom montażowym na umieszczenie większej liczby drutów na godzinę.
Telekomunikacja
W telekomunikacji owijanie przewodów jest powszechnie stosowane w nowoczesnych sieciach komunikacyjnych do połączeń krzyżowych okablowania miedzianego. Na przykład, większość linii telefonicznych z zakładu zewnętrznego przechodzi do paneli owijających w centralnym biurze , niezależnie od tego, czy są używane do linii POTS , DSL czy T1 . Zazwyczaj w głównej szafie rozdzielczej Wewnętrzne przypisania urządzeń skrośnych i zewnętrzne przypisania urządzeń skrośnych są połączone ze sobą za pomocą zworek owiniętych drutem. Owijanie przewodów jest popularne w telekomunikacji, ponieważ jest to jeden z najbezpieczniejszych sposobów mocowania przewodów i zapewnia doskonały i spójny kontakt w warstwie danych. Panele Wirewrap są oceniane pod kątem wysokiej jakości usług danych, w tym okablowania kategorii 5 . Głównym konkurentem w tej aplikacji są bloki dziurkacza , które są szybsze, ale mniej bezpieczne.
Zobacz też
Linki zewnętrzne
- [1] Karta perforowana używana do sterowania elektropneumatyczną owijarką do drutu.
- [2] Film promocyjny firmy Burroughs Corporation przedstawiający owijarkę do drutu o godzinie 09:50.
- [3] Instrukcja opisowa do powyższej maszyny, produkcji Gardner Denver .