Krosno elektryczne - Power loom
Krosno moc jest zmechanizowane krosno , i był jednym z najważniejszych wydarzeń w industrializacji z tkaniem podczas wczesnej rewolucji przemysłowej . Pierwsze krosno mechaniczne zostało zaprojektowane w 1786 roku przez Edmunda Cartwrighta i zbudowane w tym samym roku. Był udoskonalany przez następne 47 lat, aż projekt firmy Howard and Bullough sprawił, że operacja była całkowicie automatyczna. To urządzenie zostało zaprojektowane w 1834 roku przez Jamesa Bullougha i Williama Kenworthy'ego i zostało nazwane krosnem Lancashire.
Do roku 1850 w Anglii przeprowadzono w sumie około 260 000 operacji krosna mechanicznego. Dwa lata później pojawiło się krosno Northrop, które uzupełniało wahadłowiec, gdy był pusty. To zastąpiło krosno Lancashire .
Krosna wahadłowe
Głównymi elementami krosna są belka osnowy, żywopłoty, uprzęże, czółenko, trzcina i rolka odbierająca. Na krośnie obróbka przędzy obejmuje operacje zrzucania, zrywania, listew i odbierania.
- Zrzucanie . Zrzucanie to unoszenie się przędzy osnowy w celu utworzenia pętli, przez którą można wprowadzić przędzę wypełniającą przenoszoną przez czółenko. Szopa to pionowa przestrzeń między podniesioną i nienapiętą przędzą osnowową. Na nowoczesnym krośnie proste i skomplikowane operacje zrzucania są wykonywane automatycznie przez ramę żywopłotową lub healdową, znaną również jako uprząż. Jest to prostokątna rama, do której przymocowany jest szereg drutów, zwanych żywopłotami lub healdami. Przędza przechodzi przez otwory oczkowe żywopłotów, które zwisają pionowo z uprzęży. Wzór splotu określa, która uprząż kontroluje przędzę osnowową, a liczba użytych uprzęży zależy od złożoności splotu. Dwie powszechne metody kontrolowania żywopłotów to dobbies i żakardowa głowa.
- Zbieranie . Szopa jest tworzona, gdy uprzęże podnoszą żywopłoty lub zioła, które podnoszą przędzę osnowy. Przędza wypełniająca jest wprowadzana przez szopę za pomocą małego urządzenia nośnego zwanego czółenkiem . Czółenko jest zwykle skierowane na każdym końcu, aby umożliwić przejście przez szopę. W tradycyjnym krośnie czółenkowym przędza wypełniająca jest nawijana na pióro, które z kolei jest montowane w czółenku. Przędza wypełniająca wyłania się przez dziurę w czółenku, gdy przemieszcza się po krośnie. Pojedyncze przejście czółenka z jednej strony krosna na drugą jest nazywane kilofem. Gdy czółenko porusza się w przód iw tył w poprzek szopy, tka krawędź lub krajkę po każdej stronie tkaniny, aby zapobiec szarpaniu się tkaniny.
- Battening . Gdy czółenko porusza się po krośnie, kładąc przędzę wypełniającą, przechodzi również przez otwory w innej ramie zwanej trzciną (która przypomina grzebień). Podczas każdej operacji zrywania trzcina dociska lub dociska każdą przędzę wypełniającą do części tkaniny, która została już uformowana. Punkt, w którym powstaje tkanina, nazywany jest spadkiem. Konwencjonalne krosna wahadłowe mogą pracować z prędkością około 150 do 200 pobrań na minutę
Przy każdej operacji tkania nowo skonstruowaną tkaninę należy nawinąć na belkę tkaniny. Ten proces nazywa się podejmowaniem. Jednocześnie przędza osnowy musi zostać odpuszczona lub uwolniona z belek osnowy. Aby stać się w pełni automatycznym, krosno potrzebuje ruchu zatrzymania napełniania, który będzie hamował krosno, jeśli nić wątku zerwie się.
Operacja
Operację tkania w zakładzie włókienniczym wykonuje specjalnie wyszkolony operator zwany tkaczem. Oczekuje się, że tkacze będą przestrzegać wysokich standardów branżowych i mają za zadanie monitorowanie w dowolnym miejscu od dziesięciu do nawet trzydziestu oddzielnych krosien jednocześnie. Podczas zmiany roboczej tkacze najpierw używają ołówka woskowego lub kredki, aby podpisać swoje inicjały na tkaninie, aby zaznaczyć zmianę zmiany, a następnie idą wzdłuż strony tkaniny (z przodu) krosien, które mają na celu, delikatnie dotykając tkaniny. z trzciny. Ma to na celu wyczucie wszelkich zepsutych „wybrań” lub nici wypełniacza. W przypadku wykrycia zepsutych noży tkacz wyłączy maszynę i podejmie się naprawy błędu, zazwyczaj wymieniając szpulkę nici wypełniającej w możliwie najkrótszym czasie. Są przeszkoleni, że w idealnym przypadku żadna maszyna nie powinna przestać działać dłużej niż jedną minutę, przy czym preferowane są szybsze czasy zawracania.
Ze względu na sposób działania do jego obsługi potrzeba więcej niż 2 osób.
Historia
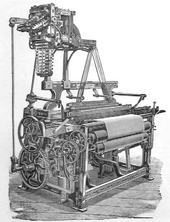
Pierwsze pomysły na automatyczne krosno zostały opracowane w 1678 r. Przez M. de Gennes w Paryżu i przez Vaucansona w 1745 r., Ale projekty te nigdy nie zostały opracowane i zostały zapomniane. W 1785 roku Edmund Cartwright opatentował krosno mechaniczne. który wykorzystywał energię wodną do przyspieszenia procesu tkania, poprzednik nowoczesnego krosna mechanicznego. Jego pomysły były najpierw licencjonowane przez Grimshawa z Manchesteru, który w 1790 roku zbudował w Manchesterze małą tkalnię napędzaną parą, ale fabryka spłonęła. Cartwright nie był maszyną odnoszącą sukcesy komercyjne; jego krosna musiały zostać zatrzymane, aby opatrzyć osnowę. W ciągu następnych dziesięcioleci pomysły Cartwrighta zostały przekształcone w niezawodne automatyczne krosno.
Te projekty poprzedzały wynalezienie latającego wahadłowca przez Johna Kaya i przeszły przez szopę za pomocą dźwigni. Wraz ze wzrostem prędkości tkania tkacze byli w stanie zużyć więcej nici niż były w stanie wyprodukować przędzarki.
Seria pierwszych wynalazców
Szereg wynalazców stopniowo udoskonalał wszystkie aspekty trzech głównych procesów i procesów pomocniczych.
- Grimshaw z Manchesteru (1790): opatrywanie osnowy
- Austin (1789, 1790): opatrunek osnowy, 200 krosien wyprodukowanych dla Monteith of Pollockshaws 1800
- Thomas Johnson of Bredbury (1803): opatrunek, fabryka 200 krosien parowych w Manchesterze 1806 i dwie fabryki w Stockport 1809. Jedna w Westhoughton, Lancashire (1809).
- William Radcliffe z Stockport (1802): ulepszony mechanizm pobierania
- John Todd z Burnley (1803): heald roller i nowe układy zrzucania, healds były połączone sznurami z pedałami uruchamianymi przez krzywki na drugim wale.
- William Horrocks z Stockport (1803): Rama była nadal drewniana, ale tokarka była zawieszona na ramie i obsługiwana przez krzywki na pierwszym wale, zrzucanie było obsługiwane przez krzywki na drugim wale, ruch pobierania został skopiowany z Radcliffe.
- Peter Marsland (1806): ulepszenia ruchu tokarki w celu przeciwdziałania złemu zrywaniu
- William Cotton (1810): ulepszenia w zwolnieniu ruchu
- William Horrocks (1813): Horrocks loom , modyfikacje ruchu tokarki, ulepszenie na Marsland
- Peter Ewart (1813): zastosowanie pneumatyki
- Joseph i Peter Taylor (1815): dwuetapowa tokarka do ciężkich materiałów
- Paul Moody (1815): produkuje pierwsze krosno mechaniczne w Ameryce Północnej. Eksport brytyjskiego krosna byłby nielegalny.
- John Capron and Sons (1820): zainstalowali pierwsze krosna mechaniczne dla wełnianych w Ameryce Północnej w Uxbridge w stanie Massachusetts .
- William Horrocks (1821): system zwilżania osnowy i wątku podczas użytkowania, poprawiający skuteczność zaklejania
- Richard Roberts (1830): Roberts Loom , Te ulepszenia polegały na nastawieniu na koło i popychacze do obsługi wielu żywopłotów
- Stanford, Pritchard i Wilkinson: opatentowali metodę zatrzymywania się na zrywaniu wątku lub osnowy. Nie był używany.
- William Dickinson z Blackburn: Blackburn Loom , nowoczesny overpick
Dalsze przydatne ulepszenia
Obecnie pojawia się szereg przydatnych ulepszeń zawartych w patentach na bezużyteczne urządzenia
- Hornby, Kenworthy i Bullough of Blackburn (1834): trzcina wibrująca lub muchowa
- John Ramsbottom i Richard Holt z Todmorden (1834): nowy automatyczny ruch zatrzymujący wątek
- James Bullough z Blackburn (1835): ulepszone automatyczne zatrzymywanie ruchu wątku oraz podejmowanie i puszczanie aranżacji
- Andrew Parkinson (1836): ulepszone nosze ( świątynia ).
- William Kenworthy i James Bullough (1841): korytarz i świątynia rolkowa (stała się standardem), Prosty ruch poklatkowy.
W tym momencie krosno stało się automatyczne, z wyjątkiem uzupełniania pasków wątku. Tkacz Cartwight może pracować na jednym krośnie z prędkością 120-130 cykli na minutę - z Kenworthy and Bullough's Lancashire Loom , tkacz może uruchomić cztery lub więcej krosien pracujących z prędkością 220-260 cykli na minutę - dając w ten sposób osiem (lub więcej) razy więcej wydajność.
- James Henry Northrop (1894) wynalazł samopowłókniający się czółenko i sprężyste szczęki wahadłowe do przytrzymywania szpulki za pomocą pierścieni na kolbie. To utorowało drogę do jego automatycznego napełniania i wymiany baterii z 1891 roku, podstawowej cechy Northrop Loom . Główną zaletą krosna Northrop było to, że było ono w pełni automatyczne; kiedy nić osnowy zerwała się, krosno zatrzymywało się, aż zostało naprawione. Kiedy na promie zabrakło nici, mechanizm Northropa wyrzucił wyczerpany pirn i załadował nowy, pełny bez zatrzymywania się. Operator krosna mógł obsługiwać 16 lub więcej krosien, podczas gdy wcześniej mógł obsługiwać tylko osiem. W ten sposób koszt pracy spadł o połowę. Właściciele młynów musieli zdecydować, czy oszczędności siły roboczej są warte zainwestowania kapitału w nowe krosno. Ogółem sprzedano 700 000 krosien. Do 1914 roku krosna Northrop stanowiły 40% amerykańskich krosien. Northrop był odpowiedzialny za kilkaset patentów związanych z tkactwem.
Krosna i kontekst Manchesteru
Rozwój krosna energetycznego w Manchesterze i jego okolicach nie był dziełem przypadku. Manchester był centrum Fustianów do 1620 roku i działał jako centrum dla innych miast Lancashire , rozwijając więc z nimi sieć komunikacyjną. To był ustalony punkt eksportu przy użyciu meandrującej rzeki Mersey , a do roku 1800 miał kwitnącej sieci kanałów, z linkami do Ashton Canal , Rochdale Canal Peak Forest Canal i Manchester Bolton & Bury Kanału . Handel barchanami dał miastom wykwalifikowaną siłę roboczą, przyzwyczajoną do skomplikowanych holenderskich krosien i być może przyzwyczajoną do dyscypliny przemysłowej. Podczas gdy Manchester stał się miastem przędzalniczym, okoliczne miasta zajmowały się tkaniem tkanin metodą gaszenia . Biznes był zdominowany przez kilka rodzin, które miały kapitał potrzebny do zainwestowania w nowe huty i zakup setek krosien. Wzdłuż nowych kanałów zbudowano młyny, dzięki czemu od razu uzyskano dostęp do swoich rynków. Spinning rozwinął się jako pierwszy i aż do 1830 roku krosno ręczne było nadal ważniejsze ekonomicznie niż krosno mechaniczne, gdy role się odwróciły. W związku z rozwojem gospodarczym Manchesteru narodził się nowy przemysł budowy precyzyjnych obrabiarek i tutaj pojawiły się umiejętności potrzebne do budowy precyzyjnych mechanizmów krosna.
Przyjęcie
Liczba krosien w Wielkiej Brytanii Rok 1803 1820 1829 1833 1857 Krosna 2400 14,650 55,500 100 000 250 000
Strategia Drapera polegała na ujednoliceniu kilku modeli Northrop Loom , które były masowo produkowane. Do lżejszego modelu E z 1909 r. Dołączył w 1930 r. Cięższy model X. Maszyny do ciągłych włókien, powiedzmy do sztucznego jedwabiu, który był bardziej podatny na pęknięcia, potrzebowały specjalistycznego krosna. Było to zapewnione przez zakup firmy Stafford Loom Co. w 1932 roku i dzięki ich patentom do asortymentu dodano trzecie krosno XD. Ze względu na swoje techniki masowej produkcji niechętnie i wolno przezbrali się na nowe technologie, takie jak krosna bez czółenek.
Spadek i odkrycie na nowo
Początkowo krosna mechaniczne wykorzystywały czółenko do przerzucania wątku, ale w 1927 roku zaczęto używać szybszego i bardziej wydajnego krosna bez czółenkowego. Sulzer Brothers , szwajcarska firma, miała wyłączne prawa do krosien bezkrętkowych w 1942 roku i licencjonowała amerykańską produkcję Warner & Swasey. Draper uzyskał licencję na wolniejsze krosno rapierowe. Obecnie postęp technologiczny doprowadził do powstania różnorodnych krosien zaprojektowanych w celu maksymalizacji produkcji określonych rodzajów materiałów. Najpopularniejsze z nich to bezczółkowe maszyny tkackie Sulzer , krosna rapierowe , powietrzne i wodne.
Implikacje społeczne i gospodarcze
Krosna energetyczne zmniejszyły popyt na wykwalifikowanych tkaczy ręcznych, początkowo powodując obniżenie płac i bezrobocia. Po ich wprowadzeniu nastąpiły protesty. Na przykład w 1816 r. Dwa tysiące zbuntowanych tkaczy z Calton próbowało zniszczyć krosna mechaniczne i ukamienować robotników. W dłuższej perspektywie, czyniąc tkaniny bardziej przystępnymi cenowo, siła napędowa zwiększa popyt i stymuluje eksport, powodując wzrost zatrudnienia w przemyśle, aczkolwiek nisko opłacany. Krosno elektryczne otworzyło również możliwości dla kobiet pracujących w młynach. Ciemniejszą stroną wpływu krosna mechanicznego był wzrost zatrudnienia dzieci w krosnach mechanicznych.
Niebezpieczeństwa
Obsługiwane przez wykwalifikowanego i uważnego tkacza, krosna nie są same w sobie niebezpieczne. Istnieje jednak szereg nieodłącznych zagrożeń związanych z maszynami, których ofiarą mogą paść nieuważni lub słabo wyszkoleni tkacze. Najbardziej oczywiste są ruchome trzciny, ramy, w których trzymane są żywopłoty oraz rolka „szczypiąca” lub „piaskowa” używana do utrzymywania szczelności tkaniny, gdy przechodzi przez przód maszyny i na rolkę. Najczęstszym urazem podczas tkania jest przyciśnięcie palców przez rozproszonych lub znudzonych pracowników, choć nie jest to jedyne stwierdzone uszkodzenie. Istnieje wiele relacji o tkaczach z długimi włosami, które wplątywały się w samą osnowę i odrywały im głowę od czaszki lub odrywały duże kawałki włosów. W wyniku tego, firmy stały się standardem branżowym wymagającym od tkaczy, aby albo trzymali włosy związane i związanymi, albo trzymali włosy krótkie, aby nie dopuścić do ich splątania. Ponadto, ze względu na możliwe zakleszczenia z przodu maszyn, luźne, luźne ubrania są zabronione. Ponadto wahadłowiec wylatuje z krosna z dużą prędkością (200+ mph / 322 kmh) i uderza w pracownika, gdy poruszająca się trzcina napotka nitkę / przędzę lub inny mechaniczny zacięcie / błąd. Jedną z komplikacji dla tkaczy pod względem bezpieczeństwa jest głośna natura, w której pracują tkacze (115 dB +). Z tego powodu jest prawie niemożliwe, aby usłyszeć osobę wzywającą pomocy, gdy jest uwikłana, i skłoniło OSHA do nakreślenia konkretnych wytycznych dla firm, aby zmniejszyć ryzyko wystąpienia takich okoliczności. Jednak nawet przy takich wytycznych urazy w produkcji tekstyliów, spowodowane przez same maszyny, są nadal powszechne.
Zobacz też
- Zgredek krosna
- Krosno żakardowe
- Paul Moody
- James Henry Northrop
- Northrop Loom
- Produkcja tekstyliów - rewolucja przemysłowa
- Bawełna - przędzenie, nawijanie, wypaczanie i tkanie
Bibliografia
Cytaty
Bibliografia
- Collier, Ann M (1970), A Handbook of Textiles , Pergamon Press, s. 258, ISBN 0-08-018057-4
- Hills, Richard Leslie (1993), Power from Steam: A History of the Stationary Steam Engine , Cambridge University Press, s. 244, ISBN 9780521458344
- Jenkins, Geraint (1972), Geraint Jenkins (red.), Przemysł włókienniczy z wełny w Wielkiej Brytanii , Londynie i Bostonie: Routledge Keegan Paul, ISBN 0-7100-69790
- Marsden, Richard (1895), Cotton Weaving: Its Development, Principles, and Practice , George Bell & Sons, str. 584, zarchiwizowane od oryginału w dniu 2018-06-29 , pobrane 2009-02-28
- Mass, William (1990), „The Decline of a Technology Leader: Capability, strategy and shuttleless Weaving” (PDF) , Business and Economic History , ISSN 0894-6825
- Miller, ja; Wild, C (2007), Rachel Newman (red.), A & G Murray and the Cotton Mills of Ancoats , Lancaster: Oxford Archaeology North, ISBN 978-0-904220-46-9
Linki zewnętrzne
Media związane z Power kręcą się w Wikimedia Commons